Knowledge Management Systems in Manufacturing Organizations: How It Works
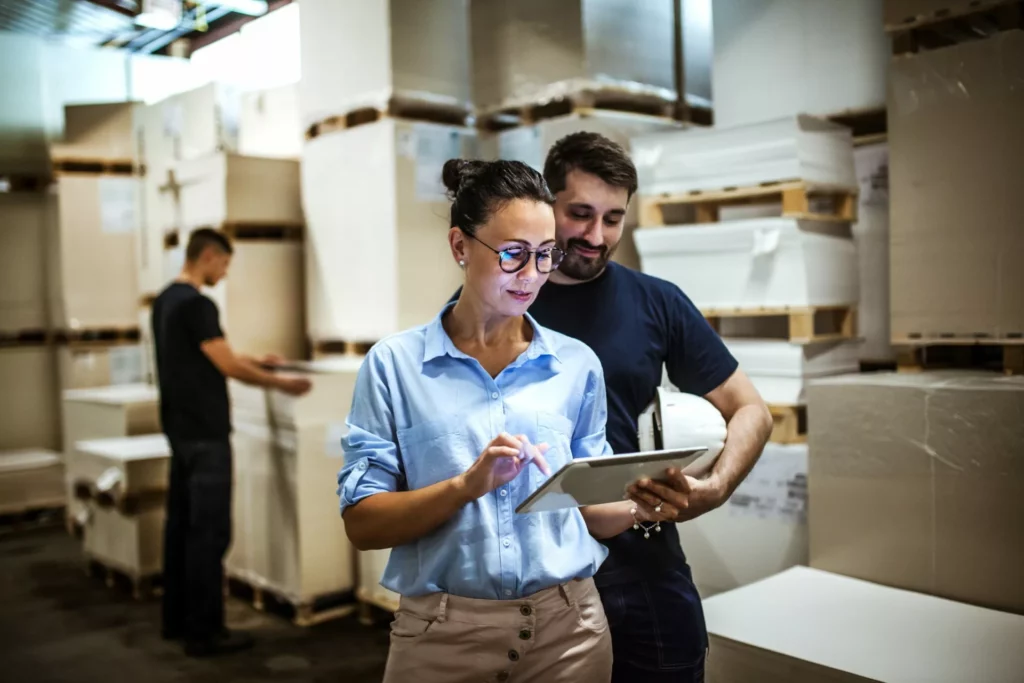
Knowledge management systems in manufacturing operate as a framework for harnessing an organization’s intellectual capital. It involves capturing, distributing, and leveraging both the explicit, documented processes and data, alongside the invaluable tacit knowledge embedded in employees’ skills and expertise. Such a disciplined approach ensures crucial information flows seamlessly across production lines and departments.
When functioning effectively, KM dramatically reduces production downtime, sharpens decision-making, and accelerates innovation in the manufacturing industry. Discover how manufacturers optimize their operations and foster a culture of continuous improvement as you read on.
Why Knowledge Management in Manufacturing Matters
The importance of knowledge management in manufacturing cannot be overstated. A knowledge management system (KMS) helps manufacturing organizations better manage and use their knowledge assets. It plays a critical role in streamlining processes, reducing waste, and enhancing product quality. Efficiently managing knowledge helps manufacturers reduce production costs and improve time-to-market for new products.
Effective KM practices contribute to risk management by ensuring that lessons learned from past experiences are documented and accessible. This helps avoid repeated mistakes and develop more robust manufacturing processes. Consequently, organizations achieve greater consistency and reliability in operations.
Knowledge management is pivotal for fostering innovation. Based on data from our Value of Enterprise Intelligence Report, research for new knowledge directly contributes to the rate of innovation. It is identified as an impact of using research in product development at a frequency of 5%.
Promoting a culture of continuous learning and sharing allows organizations to stay ahead of industry trends and technological advancements. Doing so ensures sustained growth and competitiveness in the manufacturing industry.
How Knowledge Management Helps Manufacturers
Due to the nature of manufacturing, which involves designing, creating, and managing products, several noteworthy benefits of a knowledge base in the industry exist. These include:
1. Centralizing insights
When it comes to data, manufacturers face a unique challenge. They must track not only the materials they use and the products they produce but also the machines, tools, and processes used to create their products. This data can be spread across multiple locations, making it difficult to track and manage.
Knowledge management centralizes meaningful insights from manufacturer data, making it easier to access and use. By storing insights in a central location, manufacturers can ensure that all team members have access to the latest, data-backed information at their fingertips.
Additionally, a streamlined knowledge management process enables manufacturers to track changes and updates, facilitating the identification and correction of problems. As a result, knowledge management can be crucial in helping manufacturers enhance efficiency and quality control.
2. Capturing employee knowledge
The workforce in the manufacturing industry is aging. In 2020, almost one-fourth of all employees in this industry were over 55. As employees retire, they take years of experience and tacit knowledge with them. This knowledge loss can devastate manufacturers, leading to decreased productivity and quality.
Knowledge management bridges this gap by capturing the knowledge of employees and subject matter experts within the company. Manufacturers can ensure that this information is available to future generations of employees by storing it in a central hub.
In addition, knowledge management will identify gaps in knowledge and skills, allowing manufacturers to invest in training and development programs to keep their workforce up-to-date. As the workforce ages, knowledge management will become an increasingly vital tool for manufacturers seeking to remain competitive.
3. Streamlining product development
Product development is a critical part of any manufacturing business. To stay competitive, manufacturers must continually innovate and bring new products to market. Knowledge management can play a vital role in the product development process. By organizing and sharing information about past projects, effective knowledge sharing helps manufacturers avoid duplication of effort and identify potential risks and problems early on.
Knowledge management can help manufacturers keep track of customer feedback and market trends, ensuring that new products are designed with customer needs in mind. As a result, manufacturers can streamline the product development process and bring new products to market more quickly and efficiently.
4. Standardization of processes
As manufacturers strive to improve efficiency and quality, they often look to standardize their processes. Standardization helps manufacturers improve communication and coordination between departments, reduce waste and duplication of effort, and improve quality control.
A knowledge management system can assist manufacturers in standardizing their processes by providing a central location for storing and sharing process documents. In addition, knowledge management will identify process improvements and best practices, allowing manufacturers to implement these changes quickly and efficiently.
5. Multi-location information sharing
One of the challenges manufacturers face is how to effectively manage and share information when their employees are dispersed across multiple locations. A KMS enables manufacturers to share new information in real-time. It also automatically notifies employees when new content becomes available, ensuring that all team members are aware of the latest updates.
Beyond simply sharing updates, a robust KMS also fosters a culture of collaboration and continuous learning. Employees in different facilities can easily access a centralized repository of best practices, troubleshooting guides, and project histories. This accessibility not only minimizes redundant efforts but also empowers teams to learn from each other’s experiences, leading to faster problem-solving and consistent operational excellence across all sites.
6. Minimizing information overload
A KMS helps with information overload by making it easy for people to find relevant information through keyword searches. Some platforms also allow users to filter their search results by a wide range of criteria, providing an experience similar to online shopping and eliminating the need to dig through folder after folder of content.
Aside from efficient searching, a robust KMS enables administrators to categorize content logically, tag it with relevant metadata, and establish clear version control, letting employees access the most current and accurate information. This structured approach prevents duplication and provides a single source of truth. It significantly reduces the time employees spend verifying data and increases their confidence in the information they use daily.
7. Enhancing training and development
A knowledge management system can be a valuable tool for manufacturers seeking to streamline employee training and development. It provides new employees with easy access to information about the organization and the manufacturing process, enabling them to hit the ground running. When changes are made to internal processes or technology, employees can utilize the KMS to update their training, ensuring they remain up-to-date.
With a KMS, you can house specialized technical guides, troubleshooting protocols, and best practice videos, allowing experienced personnel to deepen their expertise or cross-train in new areas. It reduces reliance on individual trainers, standardizes knowledge dissemination across the workforce, and helps ensure that all employees possess the necessary competencies for optimal operational performance.
8. Ensuring higher employee satisfaction
The 2022 State of Manufacturing report by Enterprise Minnesota surveyed employers and found that 50% cite “attracting and retaining a qualified workforce” as a big challenge to growth. A knowledge management system addresses this challenge by improving employee satisfaction. By making it easy for employees to find the information they need and providing them a platform to share their knowledge, a KMS creates a more collaborative and positive work environment.
Moreover, a study from 2024 indicates that companies with robust KM practices reported a 15% rise in job satisfaction among employees, alongside a 20% increase in productivity. This is primarily due to improved communication and enhanced learning opportunities made possible by accessible knowledge.
How to Implement Knowledge Management in Manufacturing
Successfully implementing a knowledge management strategy in manufacturing involves a structured approach that optimizes information flow and accessibility. A robust KM system can significantly enhance efficiency, reduce costs, and foster innovation within a manufacturing environment.
- Assess existing knowledge: Start identifying your organization’s current knowledge assets. Identify any gaps or areas that need improvement. This step helps clarify critical information and current management methods.
- Develop a KM plan: Create a detailed plan outlining processes and technologies for capturing, storing, and sharing information. Involve stakeholders from different departments to ensure the KM system addresses various organizational needs.
- Implement and integrate: Roll out the KM system in phases, ensuring smooth integration with existing workflows and tools. This involves setting up the chosen technology and migrating relevant data.
- Foster a knowledge-sharing culture: Encourage employees to actively contribute and utilize the KM system. Recognize and reward knowledge-sharing behaviors to embed them into daily operations.
- Invest in technology and support: Acquire appropriate technology, such as knowledge base software, collaboration tools, and document management systems. Ensure the chosen technology is user-friendly and easily accessible to encourage widespread adoption. Provide comprehensive training and continuous support to enable employees to fully utilize the system’s capabilities.
- Monitor, evaluate, and iterate: Continuously track the effectiveness of your KM strategy using key metrics. Gather feedback from users to identify areas for improvement and make necessary adjustments to optimize the system over time.
Adopting these steps allows manufacturing companies to build a dynamic knowledge ecosystem. This not only streamlines operations and improves decision-making but also cultivates a culture of continuous learning and adaptation, positioning the organization for sustained growth and competitiveness.
How Manufacturers Use Knowledge Management Software
Knowledge management applications in manufacturing and service industries are increasingly vital for maintaining a competitive edge. In manufacturing, a KM system supports supply chain management, product development, and quality control by providing real-time access to critical information. Knowledge management practices have seen success in the following aspects of manufacturing:
1. Manage supply chain and vendor information
One of the most helpful features of a KMS is its ability to manage supplier information. In today’s globalized economy, manufacturers frequently source materials from around the world. This can make it challenging to keep track of supplier information, such as contact details, delivery times, and pricing.
A knowledge management system centralizes this information, making it easier for manufacturers to find the suppliers they need when they need them.
2. Ensure adherence to safety regulations
Manufacturers must be vigilant in managing safety data and complying with government regulations. Knowledge management software can play a vital role in helping manufacturers to meet these obligations. The software can be used to centralize safety protocols, training materials, video guides, and more.
3. Set up training and onboarding processes
With a KM platform, you can streamline the training and onboarding process by providing a hub for training materials. Employees can access these materials at any time, from any location. Additionally, manufacturers can utilize knowledge management software to hold employees accountable for reviewing essential information and identifying knowledge gaps or areas where further training is required.
Utilizing the knowledge housed in the KMS can also enhance the overall efficiency of the training process. Manufacturers can leverage knowledge management software to ensure that all employees are properly trained and prepared for their job duties.
4. Collect product design and development information
Knowledge management software can serve as a central repository for all product design specifications, engineering drawings, material data, and research & development findings. This ensures that design teams have immediate access to the latest versions of documents, historical design choices, and accumulated technical expertise, accelerating innovation and reducing design errors. It also facilitates collaboration among diverse engineering disciplines.
5. Standardize quality control and assurance
Maintaining high product quality is paramount for manufacturers. A KMS can centralize quality standards, inspection procedures, testing protocols, and historical defect analysis reports. This enables quality assurance teams to quickly access relevant guidelines, document non-conformities, and share corrective actions across various production lines, resulting in consistent product quality and adherence to industry standards.
It’s clear that KM software extends to other parts of the business. For instance, in the service industry, KM applications enhance customer service and support by ensuring that employees have the necessary information to address customer inquiries effectively. They also facilitate the sharing of best practices and lessons learned, which can lead to improved service delivery and customer satisfaction.
Both knowledge management in manufacturing and the service industry benefit from KM applications that integrate with existing information systems, providing a seamless flow of data across the organization. This integration enables more informed decision-making, helping organizations respond quickly to market changes and customer demands.
Examples of Successful Knowledge Management Systems in Manufacturing Organizations
Several organizations have successfully implemented knowledge management systems, reaping significant benefits in terms of efficiency, innovation, and customer satisfaction. Below are a few examples:
- Parts Town: Parts Town implemented a KM system to centralize critical information, including technical manuals and training materials. This has significantly reduced search times, improved response accuracy, streamlined onboarding for new employees, and facilitated seamless knowledge transfer and collaboration across teams and with manufacturer partners.
- Toyota: Known for its lean manufacturing principles, Toyota has a robust KM system that emphasizes continuous improvement and employee empowerment. The company also fosters a culture of knowledge sharing, allowing the brand to maintain its position as a leader in the automotive industry.
- Siemens: This global technology company uses KM to streamline operations and drive innovation. Siemens’ knowledge management initiatives have led to increased collaboration and the development of cutting-edge solutions across its diverse business units.
These examples demonstrate the transformative impact that effective knowledge management can have on organizations across various fields within the manufacturing industry. Such systems enable companies to optimize not only their internal processes but also significantly enhance their competitive edge in a rapidly evolving global market.
Choosing the Right Knowledge Management System for Your Manufacturing Business
When selecting a knowledge management system for your business, it’s essential to consider the size of your company and the specific needs of your employees. For example, if you have a large workforce spread out across multiple locations, you’ll need a KMS that all employees can access regardless of their location.
You’ll also want to consider how much information you need to manage and the complexity of your processes. Additionally, it’s essential to select a KMS that integrates with your existing systems, allowing employees to access knowledge seamlessly within the flow of their work. Once you’ve considered these factors, you can narrow your options and select the best KMS for your manufacturing business.
Key Components of a Manufacturing Knowledge Base
A successful manufacturing knowledge base consists of several key components that work together to facilitate the effective management of information. Below are the critical elements you should consider when building your knowledge base:
- Content management system (CMS): A robust CMS is essential for organizing and storing information. It should allow for easy retrieval and updating of content, ensuring that employees have access to the most current data.
- Collaboration tools: Tools that enable seamless communication and collaboration among team members are vital. These can include chat applications, project management software, and forums for sharing ideas and feedback.
- AI enterprise search functionality: An intuitive search feature powered by artificial intelligence (AI) is crucial for quickly locating specific information within the knowledge base. This reduces the time spent searching for data and enhances productivity.
- Training and development resources: Providing access to training modules and development programs within the knowledge base helps employees continuously improve their skills and knowledge.
- Analytics and reporting: Implementing tools that track usage and engagement with the knowledge base can provide valuable insights into how information is being utilized and where improvements are needed.
Securing these fundamental components ensures a dynamic and accessible knowledge base. This empowers manufacturing organizations to streamline operations, foster continuous learning, and make more informed decisions, solidifying their competitive advantage and adaptability in a complex industrial landscape.
Frequently Asked Questions
What are the core principles of knowledge management in manufacturing?
The core principles of knowledge management in manufacturing revolve around systematically capturing, organizing, and disseminating vital information throughout an organization. This ensures that critical data, best practices, and lessons learned from production, design, and operational processes are accessible to all relevant personnel.
Can big data and knowledge management manage inventory and shipping?
Big data analytics can process vast amounts of real-time information from sales, supply chains, and logistics to predict demand, optimize stock levels, and identify shipping efficiencies. Knowledge management then provides a structured framework and accessible insights derived from this data. It empowers decision-makers with best practices, historical trends, and operational guidelines to ensure timely deliveries and minimize warehousing costs.
How is AI influencing the future of knowledge management in manufacturing?
AI is fundamentally reshaping knowledge management in manufacturing industries by intelligently processing and synthesizing complex information for immediate use. It empowers advanced search, personalizes knowledge delivery, and facilitates predictive insights, allowing companies to anticipate needs and make proactive decisions.
The Future of Knowledge Management in Manufacturing
As the manufacturing industry continues to evolve, the role of knowledge management will become increasingly critical. The future of KM in manufacturing lies in leveraging cutting-edge technologies, such as artificial intelligence and machine learning, to further optimize processes and decision-making. When embracing KM practices, manufacturers can enhance efficiency, drive innovation, and maintain a competitive edge in a rapidly changing market.
Enhance Manufacturing with KM
Learn how Bloomfire’s KM solutions can boost efficiency in manufacturing industries.
Learn MoreHow to Navigate the Chain of Command in Business to Get Executive Buy-in
Knowledge Management Cycle: From Theory to Real-World Implementation
5 Signs of Information Hoarding at Work
Start working smarter with Bloomfire
See how Bloomfire helps companies find information, create insights, and maximize value of their most important knowledge.
Take a self guided Tour
See Bloomfire in action across several potential configurations. Imagine the potential of your team when they stop searching and start finding critical knowledge.